So how do MHEVs differ from a traditional ICE vehicle. In this second blog on the electrification of the powertrain, we dig into some of the key differences in terms of architecture.
The days of the internal combustion engine (ICE) are numbered. Well certainly you can be forgiven for thinking that given the number of major cities and even some countries talking about banning all diesel and petrol automobiles within the next 15-20 years. But hang on, is it really that easy to swap every vehicle with an electric equivalent? Of course, not. If it was, everyone would already be driving a fancy Tesla and hoping we don’t collide with a pedestrian or cyclist because of its extremely quiet electric motors.
Jokes aside, there are many challenges impeding the faster spread of electric vehicles (EV). From vehicle cost, charging infrastructure, power generation demand and range anxiety, to consumer behavior and attitudes to the new technology along with legal and insurance concerns. While these issues may take a decade or two to be fully sorted out, the regulations being imposed to curb carbon dioxide (CO2) emission are forcing vehicle manufacturers to come up with alternative, cost-effective, pragmatic solutions.
In my previous blog, I briefly stated that mild hybrids (MHEV) and full hybrids (HEV) are stepping stones towards full vehicle electrification. This is mainly due to the high battery costs in full electric vehicles and the time pressure imposed on manufacturers. While batteries are gradually getting cheaper (by approximately 8% per year according to the US Department of Energy) mass market EVs are not the short-term solution that CO2 regulation institutions are looking for, especially in Europe and China.
How MHEVs differ from ICE vehicles
So how do MHEVs differ from a traditional ICE vehicle. To start Figure 1 highlights the main system changes applied in an MHEV. The most obvious difference between a conventional vehicle and the mild hybrid is the addition of a 48-volt battery.
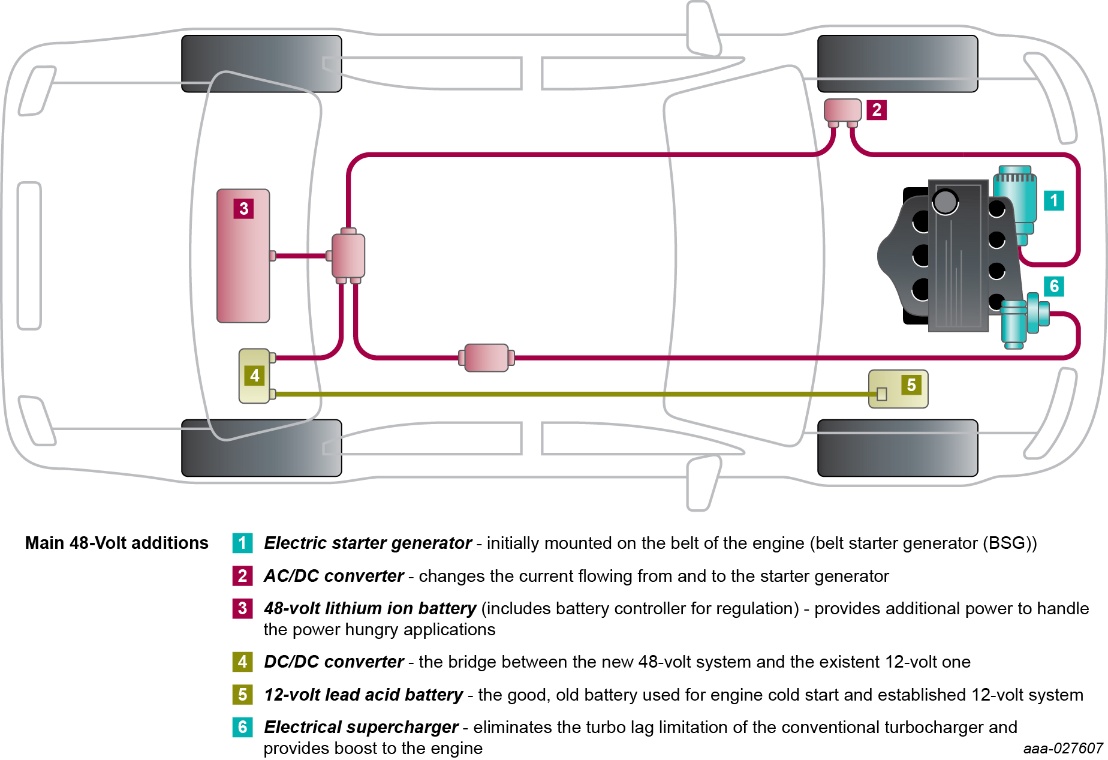
Figure 1: 48-volt architecture
The main purpose of the 48-volt battery is to provide the additional power demanded by power-hungry applications as well as reducing the electrical current throughout the system. This trick allows for smaller cable cross-sections to be used, massively cutting the amount of copper in the 4+ kilometers of wiring in today's high-end vehicles. And therefore enabling significant weight and cost reductions. Other notable differentiating factors of mild hybrid are the new 48-volt modules such as the electric starter generator, electrical supercharger and DC/DC converter. The latter simply converts the 48-volt battery power to support established 12-volt applications in the vehicle.
Starter generators and superchargers
The 10 kW (or higher) starter generator is a very valuable 48-volt system addition and offers multiple functions. Firstly, it acts as an alternator (converting mechanical energy into electrical) and is connected to the crankshaft of the engine. Secondly, it boosts the engine to increase the vehicle’s acceleration performance and manages engine load to reduce fuel consumption. Lastly, when the vehicle is cruising or decelerating/stopping the starter generator can recover electrical energy back to the battery. Currently there are a few different architecture topologies, each of which provide a certain level of CO2 benefits.
Looking somewhat like the shell of a snail, the other main 48-volt addition is the electric supercharger. Its primary purpose is to increase the air/fuel mixture density that goes into the cylinder of the engine. Thus, more power is output from the engine without increasing cylinder size. With this capability, the supercharger effectively contributes to the fuel economy of the mild hybrid.
What to do with all that energy
Of course, all this extra power still needs to be used efficiently, and not all vehicle systems need to be powered with 48-volts. From a pure power perspective, high power applications such as the starter generator, supercharger, DC/DC converter and A/C compressor would be the first to be ported across to the 48-volt supply network. Figure 2 shows Nexperia’s view of which applications have the potential to transition to the higher voltage side.
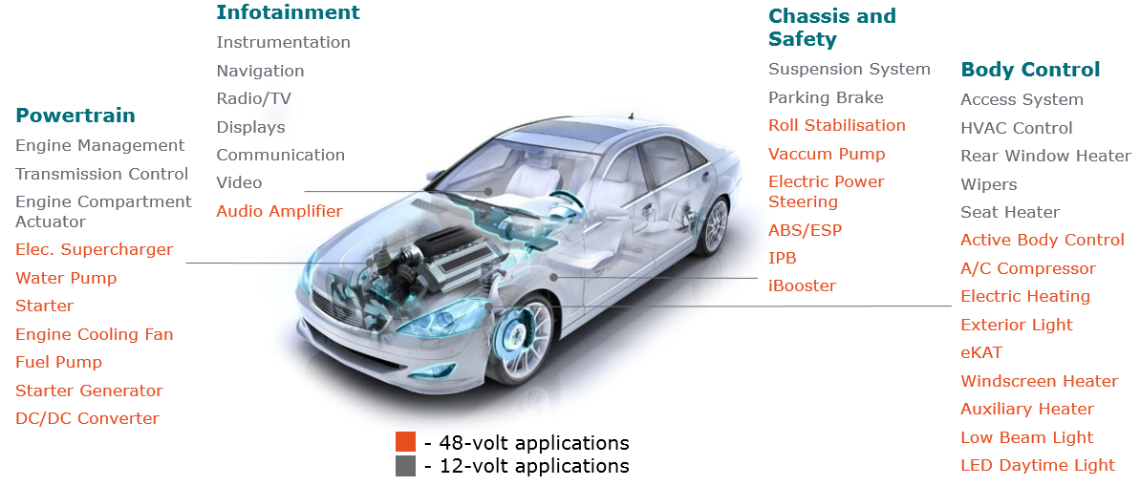
Figure 2: 12-volt to 48-volt application transition
These are certainly exciting times for the automotive industry and developments to combat CO2 emissions ahead of full EV adoption are worth following closely. The hunger for more power and the urge for emission-free vehicles means automotive players are putting their foot on the innovation gas pedal.
In the next chapter, I’ll dive into more detail on the starter generator and look at its power requirements, application topologies and much more. Stay tuned!