The first in a series of blogs looking at the electrification of the powertrain, the different solution architectures and what that means for power semiconductors.
Electrification of the powertrain – introduction
Vehicle electrification has recently started to pick up aggressive speed in the automotive industry. The main drivers of this phenomena appear to be based around clean driving, decarbonisation, air quality and health in the urban environment. Often implemented through emission reduction requirements agreed locally or between governments and relevant organisations across the globe, these regulations require a quick response by the automotive OEMs to reduce the carbon footprint of their vehicles and avoid potentially heavy penalties.
The fundamental change is away from reliance on the conventional internal combustion engine (ICE) to some form of electrical powertrain. Multiple powertrain solutions are being implemented respective to the separate OEMs’ strategies, visions and financial capabilities. This has led to a plethora of new terminology within the industry. At first glance it can be bewildering, especially as new energy vehicles start to hit the roads in greater numbers. The most popular powertrain solutions being mentioned are: 48V mild hybrid (MHEV); full-hybrid (HEV); plug-in hybrid (PHEV); battery electric (BEV); and fuel cell (FCV).
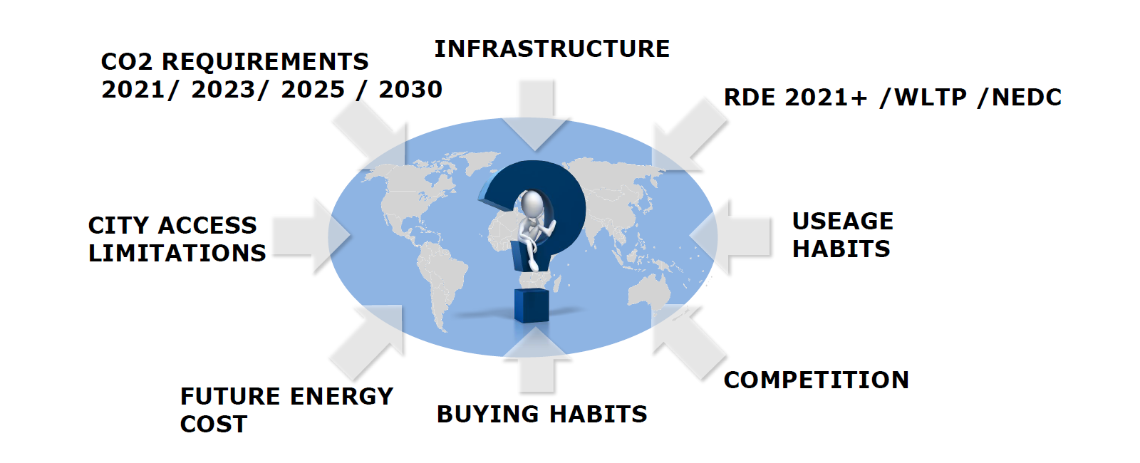
Figure 1. Electrification drivers and factors Source: AVL
Each one of these types has a specific architecture as well as individual operational and power requirements. Furthermore, the achieved carbon dioxide (CO2) reduction differs vastly, ranging from approximately 15% for 48V MHEVs to 100% for BEVs and FCVs. These details need to be carefully considered and analysed by the automotive tier 1s, who directly supply the OEMs with the relevant automotive systems and parts (DC/DC converter, battery management system (BMS), inverter, etc.).
Among the key questions that all players in this industry would love to have the answer to, is which vehicle / powertrain type(s) will be the most dominant (both short term and long term) and when will the tipping point arrive for mass adoption. This is essential to develop a successful strategy and increase market share in the business. During most of the recent conferences people have been talking predominantly about 48V MHEVs and how they represent a stepping stone towards the complete vehicle electrification. I have also heard a lot about BEVs being the end goal of this journey. Whilst this may be true, there are certain challenges which must be mentioned and considered.
In a nutshell, while solutions such as 48V MHEV and HEV are currently acceptable, long term they cannot offer a satisfying CO2 reduction and driver experience. Inversely, these partially electrified vehicles are relatively cost-effective to develop as they are close to the well-known conventional vehicle making it easy for OEM’s to implement within their existing manufacturing base. A simple evolutionary step.
End-game vehicle solutions such as BEVs and FCVs can solve the CO2 emission drama (at least in terms of vehicle emissions) while also providing customers with an entirely new driving experience (e.g. instant torque (BEV), autonomous driving functions, etc.). The main challenge for those vehicles is the high cost of production – battery cost (BEV), production of hydrogen (FCV), etc. – and manufacturing capacity to supply the millions of batteries needed for mass adoption. Furthermore, there are external challenges such as the charging infrastructure and power distribution which need further development to meet vehicle demand for electricity and allay consumers fears.
In this blog series, I will attempt to delve deeper into each of the main vehicle types to further understand their architecture, system requirements and specifically what that means for power semiconductors. In the next instalment, I will cover 48V MHEV where we will explore the first baby steps towards a clean driving