Dilder Chowdhury has worked in semiconductors for over 24 years, first joining Nexperia’s Innovation team, then moving to Marketing and the role as Architect for Power GaN technology in Manchester. His current role is Director, Strategic Marketing for Power GaN technology.
His job encompasses everything from device physics down to packaging and end-products, where Nexperia investigates and combines all the value that our company can add to the offering of GaN and GaN-related packages, products and modules. It is a strategic approach designed to bring the best without compromising the robustness and quality.
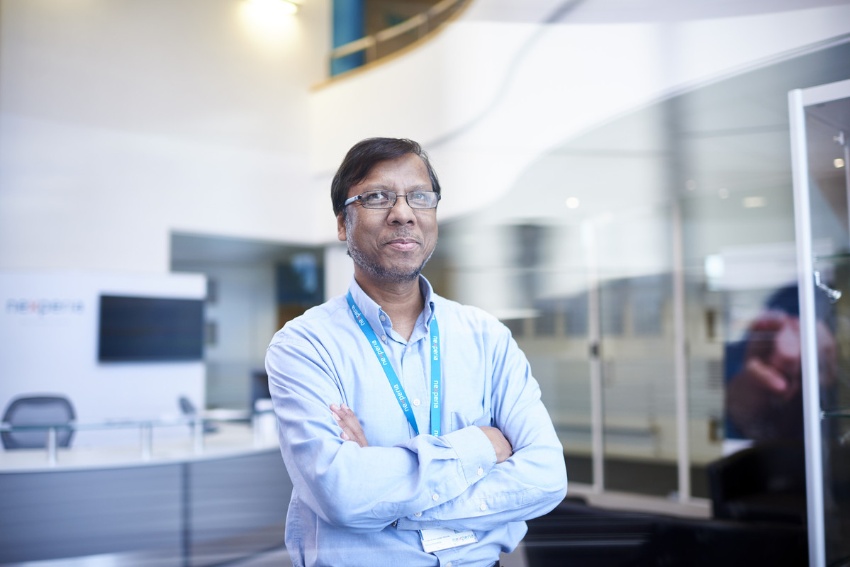
Nexperia is a trailblazer in GaN, not just in products, but production too. Can you tell us how?
Our production needs to be the best value for money; we are a company working heavily in automotive, so we need to maintain the highest levels of quality for whatever the new technology we introduce. We cannot compromise on quality, it’s non-negotiable. We are established semiconductor company with over 90 Billion semiconductor devices sold every year with a track record of quality products. Power GaN technology is new compared to our Si technology. There are many challenges : from epi material, fab processing and volume production. We will maintain the same quality and robustness on every stages of innovation and production processes using our in house quality processes in place. We’ve introduced our first product with AEC-101 level quality and bringing our in-house SMD package CCPAK(Copper clip packaging technology) to maintain full control of our production process with the aim to volume capacity implementation. We are introducing our products to industrial, datacenters and telecom infrastructures followed by automotive segment with in-house front and back end operations. Our capacity plan is in place for volume production.
Is there a threshold, a level when you can’t improve any further?
We don’t believe so. While one technology(Si) may be reaching close to the limit, there are other technology (GaN, SiC) opening up further improvements. That’s why, in a sense, we’re seeing that silicon is reaching a limit and leading us to move to Gallium Nitride. In silicon for high voltage, there is little room for improvement. In power, it’s about performance, and silicon is reaching a plateau. Early electric vehicle systems were predominantly silicon-based, but we’re trying to bring GaN in, which gives extra mileage which silicon can never reach.
Extra mileage from GaN? You mean bigger batteries?
It’s more fundamental, you have to look at switching losses to see. Consider the current voltage crossover during every switching cycle, you get crossover losses, you have interference during transition, and you have losses. If you can create a situation where the voltage falls to zero and current rises to max and there is minimal overlapping, then your switching losses are close to zero. Thus your efficiency is maximized, your battery life is maximized, and improved by around 10%. That’s where GaN comes in. Power GaN can offer significant reduction in switching losses and hence battery charge lasts longer.
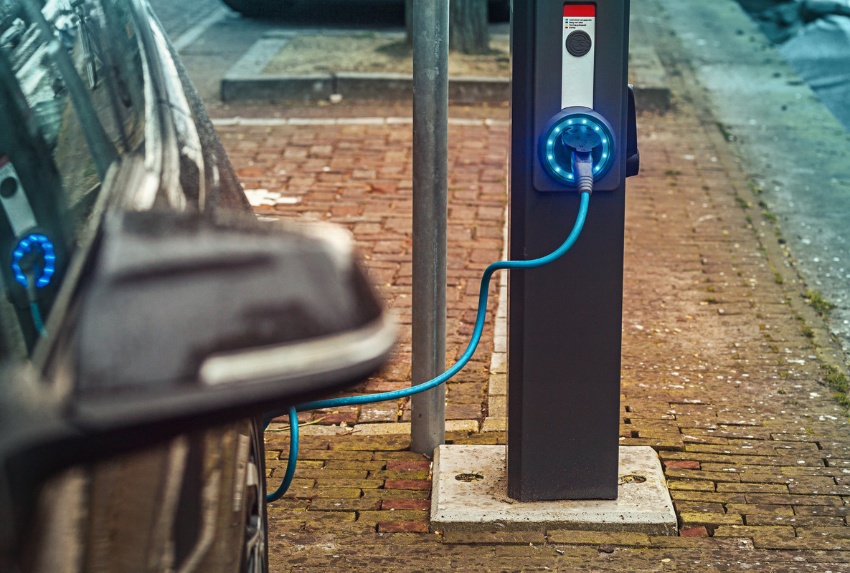
Power and efficiency then, how does GaN win over silicon?
Consider the power conversion from the battery to the motor that drives your wheels, where you convert electrical to mechanical energy, so the efficiency of the motor itself matters. If you exclude the battery, and just look at the path from the battery to the motor, it’s all electronics. Here is where we can make real gains. At present, the efficiency of this transfer is around 92%. If you have a 100 kW motor, 92% efficiency means 8kW of heat is generated through thermal loss. An electric kettle is 2kW, so you’re sitting on top of a lot of heat. So, you have to cool it, which takes extra energy or water cooling. But let’s say then that you could get to above 98% efficiency.
Your losses are reduced to one quarter, you only have 2% losses, that’s 2kW heat, which can likely be air-cooled. A move from silicon to GaN can make this happen. Not only will you reduce losses, you simplify the system and your whole system size gets smaller and lighter so you can get more mileage, so there are lots of indirect benefits.
Why hasn’t it happened sooner?
GaN is only coming to the market now. It’s been in research for last 30, 40 years but it was never practical. It works in the RF segment, Radio Frequency, in for instance 4G and 5G base stations, which already have GaN. But in the power segment, GaN wasn’t viable because of cost. People said they could tolerate a little loss of power, if there was a gain on cost – the loss was acceptable. So, they said they’ll live with the loss until this extraordinary technology comes within their buying capacity. So, it needed to be commercially viable as well as suitable for purpose, and we’re getting there. GaN on Si has a better viable cost roadmap.
Where is GaN now?
It’s a disruptive technology in its inflection point, already past the early adopters, so now we’re in an uptick, with the initial volume expected to come from high-performance applications. Production-wise, although there are different internal processes in manufacturing GaN, we use the same production systems that we have perfected with our knowledge of silicon. GaN wafers vs silicon wafers are different of course, which means they will be different to use on the customer side too. We’re looking to adapt much of the process and make this work. It’s incredibly rewarding because it takes every bit of knowledge and understanding from the whole team working on this, but, we know it’s possible, we know it’s achievable.
How is Nexperia ahead with GaN?
We’ve been working in the background with GaN for a while. We sell around 90 billion products a year from a portfolio of 17,000, but only one of them so far is GaN that’s released but few in the pipeline. It’s a disruptive technology and we’re using research and proof to break down people’s concerns about it. The principle focus for Nexperia in GaN is in the electrification of vehicles, reducing carbon dioxide emissions, reducing losses, all this towards a greener future. And in an electric vehicle you need an onboard charger, a DC/DC converter, because you have a 12V / 48V / 400V battery, each of these has to be able to work with each other. And you need a plug so you can charge your battery, you need an inverter, in all of these you need efficient conversion. And our plan is for all of these conversions to be based on GaN.
What’s next?
When GaN comes, you can run at higher frequency, which means your magnetics are smaller while still keeping the losses small, your adapters are smaller, things are lighter, and things are more efficient. The power converter, from the battery to wheels, that might take a couple of years because we’re working on an evaluation version now, to showcase to the world that GaN is here. We’re way past theory. We’re in new technology, a blue ocean program – exploring a new territory, we’re pioneers, nobody has been here.
Today there are a lot of companies looking to other territories, such as Silicon Carbide, which is at a more mature production stage than GaN. But we’re working to accelerate past Silicon Carbide. All three technologies will coexist, as semiconductor history suggests that people still use old technology. But this is a new horizon that makes things possible that simply weren’t possible with the old tech.