For the last decade or so, when it came to power MOSFET advances the primary goals were to push up efficiency and drive down drain-source on resistance. For most applications, choosing a given Figure of Merit (RDS(on) x Qg) was usually a good starting point. As technologies have advanced and applications become more complex, simply looking to the FOM no longer ensures the best MOSFET for the job. In fact, it is becoming increasingly necessary to optimize a growing set of MOSFET parameters to best match those requirements, often at the expense of traditionally important parameters.
This time last year, in the blog “Is today’s accepted MOSFET Figure of Merit still relevant?” it was argued that with new power technologies and faster switching topologies we are seeing numerous different parameters become ‘system critical’. One example given was that for SMPS topologies we need to realize how important Qrr is, and how Qg is becoming ‘less’ critical.
As we look at the broad power MOSFET application range it is clear that this trend is being felt in an increasing number of applications. For many designs that means simply choosing a standard MOSFET with the right FOM no longer fulfils all the application requirements. Those requirements could include managing voltage spiking, reliable linear mode performance, enhanced protection or EMI signature to name just a few. Suddenly a whole new range of MOSFET parameters such as Safe Operating Area (SOA) become crucial to that specific application. And to optimize those parameters can quite often have a direct negative impact on the more traditionally important parameters.

A portfolio that has grown organically
At Nexperia we have been combining our proven MOSFET expertise and broad application understanding to address very specific demands from our key customers for some time. That has led to a different approach to number of developments in recent years and the beginnings of our Application Specific MOSFET or ASFET families. Developments such as our ASFETs for Power over Ethernet (PoE) and power sourcing equipment (PSE) as well as our ASFETs for Hotswap and Soft Start that support always-on rack-based computers, communications and storage systems. Among the parameters important to both these applications are a low RDS(on) and enhanced Safe Operating Area (SOA) – two parameters which in normal MOSFETs are mutually exclusive.
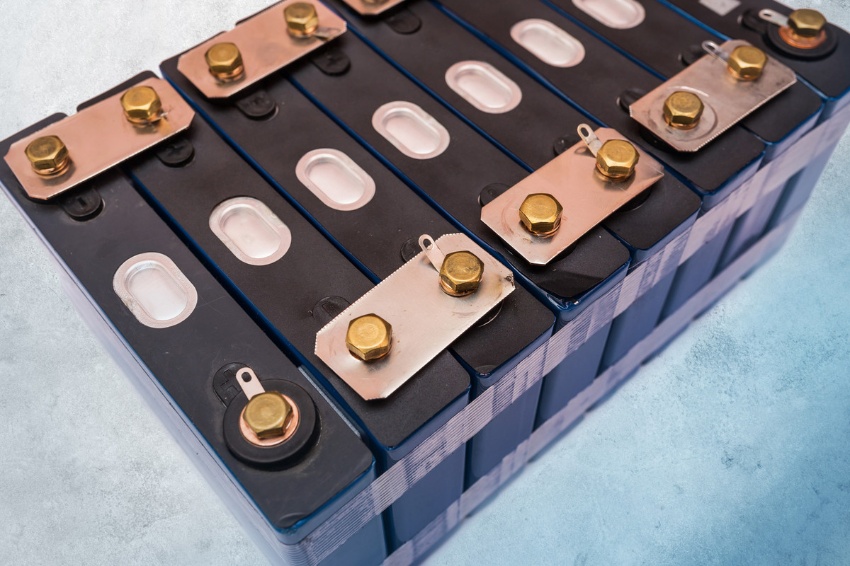
Building on this application specific approach with customers we started looking at what other applications and ‘system critical’ parameters could be optimized. Drawing on Nexperia’s SOA and robustness optimizations we were able to develop ASFETs for Battery Isolation designed for multi-cell lithium-ion battery packs. This ensures any significant discharge caused by a fault condition is managed in a controlled manner until the battery is safely isolated and the system switched-off. While a low RDS(on) is required for low conduction losses in normal operation, in terms of functionality the parameters for safe battery isolation are paramount.
The growth of DC motor control
Possibly one of the best visions into how the power electronics market has changed over the last few years has to be the revolution we have witnessed in DC motors. From the relatively large inefficient devices they used to be, to the extremely small and powerful PWM driven brushless DC motors we have today is remarkable. Not only have the DC motors changed, but they have also made a whole range of new applications possible, using either 24 V rails or multi-cell lithium-ion battery packs.
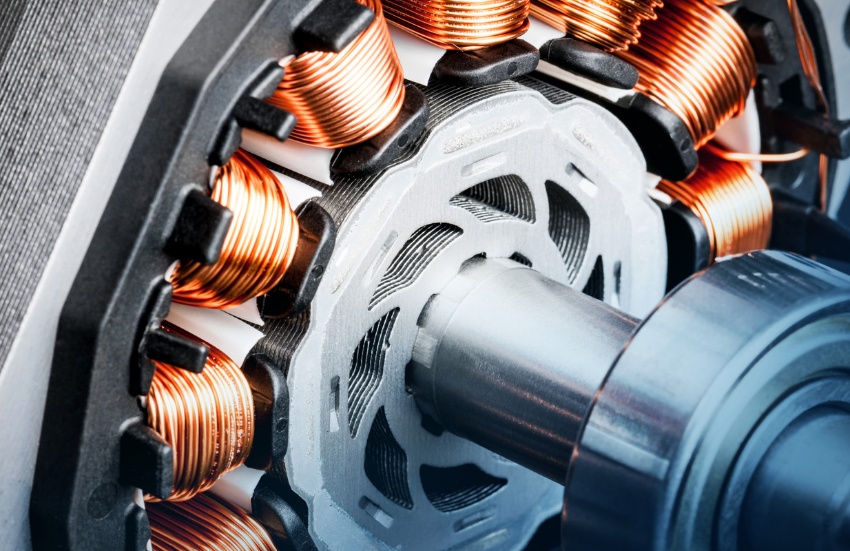
But of course, with such a diverse range of applications (drones, household appliances and power tools right up to golf carts and forklift trucks) there is an equally diverse range of optimizations required within our ASFETs for DC Motor Control family. For example, fitting the power and efficiency required into the small compact bodies of cordless power tools can be challenging. So, optimizing the MOSFET to handle a current drain of up to 300 A in a Power-SO8 package (LFPAK56), provides sufficient protection during high-torque start-up situations or fault conditions. Alternatively, balanced current-sharing can be key for large multi-cell mobility systems where multiple MOSFETs are used in parallel.
Addressing classic and upcoming applications
As designers continue to push the boundaries of application performance, it is increasingly crucial to understand how the MOSFET will be used. This is clearly highlighted by the few examples mentioned above, but at Nexperia we believe more applications will require some level of optimization to meet their different requirements.
That could be something as relatively straightforward as optimizing VDS for the growing number of 36 V DC motors appearing in everything from chainsaws and hedge-trimmers to ebikes and scooters. Or optimizing MOSFETs to comfortably handle repetitive avalanche currents while maintaining a junction temperature below 175 °C, so that designers using inductive loads, such as driving solenoids, have a modern replacement for planar technology. Whatever the optimization, for many applications simply choosing a MOSFET by its figure of merit is going to become increasingly challenging.
For more information including datasheets, videos and other useful background information, check out the Application Specific MOSFETs product category.