Tim Crispin, our MOSFET quality guru, looks at what quality means today in terms of how we achieve defect rates in the parts per billion range and the drive towards zero incidents.
At Nexperia, we pride ourselves on our record in quality. We are automotive qualified, compliant with all the relevant standards, and on a continuous drive for zero defects, just like every other semiconductor supplier. We all say this because we know our customers need to hear it. However, the industry has moved far beyond the point where that is enough to be considered a quality supplier.
Across our portfolio, we currently run at quality levels better than 1 part per million, with some product lines at a few parts per billion. To improve on that kind of performance, traditional quality methods just aren’t going to cut it. You need to look at quality in a whole new way.
It’s about incidents
Naturally we are constantly trying to improve our quality performance. Trying to eliminate every individual failure at customers before it occurs. But in truth the goal of zero defects is an old-fashioned concept. With the level of quality at which we are currently operating, customers become extremely concerned by quality incidents, where a manufacturing lot has two or more defective products. So, we track on zero incidents.
It’s about people
Research by one of our customers found that over half of all incidents can be traced back to a person and a series of mistakes or decisions they made. Quality is a human issue. This isn’t something you can change by throwing money at it. If you automate a process you just transfer the quality issue from the person doing the process to the person maintaining the equipment. There is always a human behind it, and any efforts to push quality further need to be human driven.
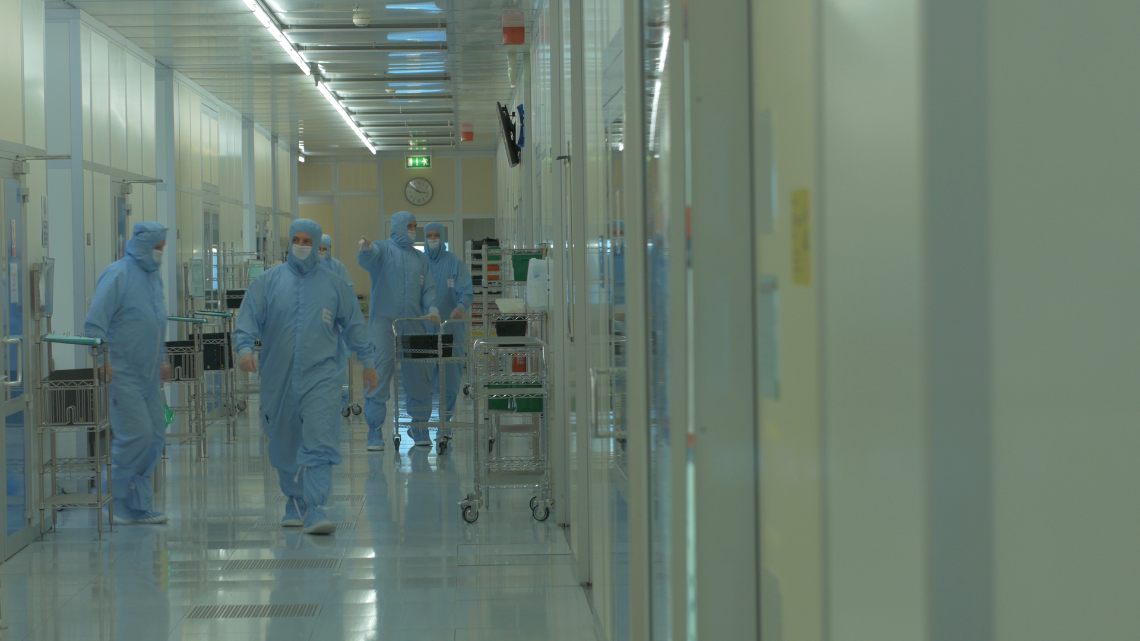
It’s about management
So most quality incidents come back to a person. But ask yourself, what were the personal circumstances behind the error that led to the incident? Perhaps the person’s decision made sense at the time because they didn’t have all the information they needed. Maybe the mistake came because they were overloaded or distracted and couldn’t give the task the full attention it required.
Therefore, reducing incidents is primarily about management: giving people the time to really understand the processes and equipment they use, and ensuring they are never under too much pressure to do their job properly.
For example, at our facility in Manchester, we have introduced new measures for tracking quality performance that focus on employee loading, such as overtime and how many interventions our process engineers need to make. We’ve also built more time into our working schedules to allow engineers to share their own experiences. Too often the factory had the knowledge to prevent incidents, but it only becomes effective if you can make it available to everyone when it matters. Traditional knowledge databases don’t work, giving people the time to talk to and train each other does.
It’s proactive
It is nearly always possible to track down the root cause of a quality incident, so it doesn’t happen again. But then you’ve already had an incident. We want to stop incidents happening in the first place. That takes a new mindset, especially as you have limited freedom to change things within the semiconductor manufacturing process. So you need to think outside the box.
One way we do that is by creating scenarios either individually or in brainstorming sessions, and asking ourselves what set of circumstances could cause that. Another is to have people from different areas of the factory visit other workspaces to see what potential issues they can spot and how we can address them. Many of the things seem quite obvious afterwards, but in the heat of pressure of the day-to-day job they get overlooked. Sometimes, it takes a fresh, external view.
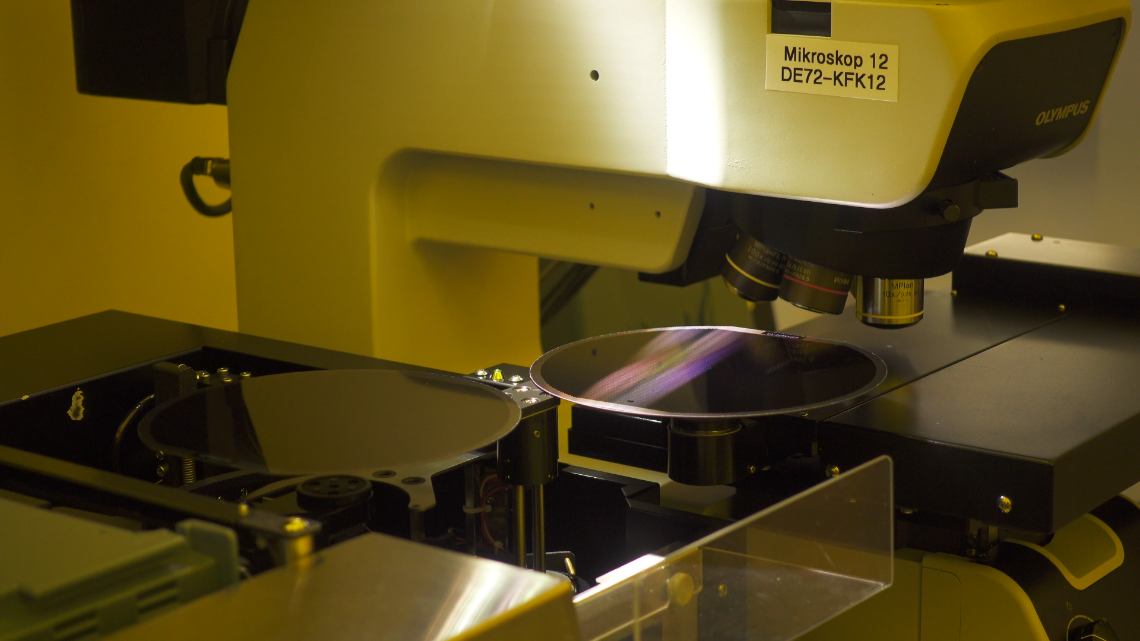
It’s about making life easier for our customers
Fundamentally, the Nexperia approach to quality is about making our products as easy as possible for our customers to use. Of course, eliminating incidents is one way of doing that. But our customers are also constantly looking to reduce costs by speeding up their own processes – for example by re-flow soldering at faster speeds and higher temperatures.
That puts greater stress on the components they use. At Nexperia, we take great pride in looking beyond product and quality specifications to make our products as robust as possible. We do everything we can to put our customers’ problems inside our own firewalls. For example, we supply individual components, but our customers use those components mounted on boards. So, as well as our standard product testing and evaluation, we also evaluate our products on the boards our customers use to preempt anything that might occur and resolve it before the customer.
It’s about supporting business success
Working this way, makes quality one of the leading drivers for sales, ensuring Nexperia’s continuing success.