In 1969 the first device housed in the breakthrough SOT23 plastic surface mount package rolled off the assembly line. Last year Nexperia alone shipped over 30 billion SOT23 packaged devices. These two facts highlight a key challenge of semiconductor innovation, balancing the demand for change with the need for consistency.
Semiconductor developments regularly have to bridge opposed ideas. The need for proven solutions against the demand for new innovation. The drive for ever smaller and faster versus reliability and consistency requirements. Pressure to increase functionality while minimizing system redesigns. The fine balance that needs to be struck to reduce costs while improving quality. All of these points can be seen in the life of the industry’s favorite surface mount transistor package – the SOT23.
A star is born
The idea of replacing ‘thru-hole’ packages with surface-mount devices first came in the 1960s. In April 1966 Piet van de Water started sketching what would become the 23rd Standard Outline Transistor or SOT23 package for Philips. Following pilot line development in Nijmegen during 1968, the first SOT23 plastic encapsulated device would roll off the Hamburg production line in 1969 – and a star was born.
As with any technology breakthrough, success was not overnight. In fact, it wasn’t really until the boom in consumer electronics in the 1980s and early 1990s that surface-mount technology (SMT) truly started to make its mark. The SOT23 quickly became the de-facto standard for a three-pin surface mount package. Nowadays virtually all electronic hardware is manufactured using SMT, although for certain products and applications thru-hole packages remain very popular, particularly for product development and breadboarding.
Building a legacy
While the SOT23 has been a constant for the last 50 years, it too has moved with the times. From adding the 5-pin variant and going lead-free (Pb) to the more recent expansion of operating temperature range to 175 °C, this industry favourite continues to evolve.
Demand for higher packing densities also led to a number of offspring – such as the SOT223 and SOT323. Essentially if you look at any small pin-out surface-mount SOT package, you will quickly see the family resemblance to the SOT23.
The push for ever greater efficiency and quality has driven innovation in production methods and the equipment needed to manufacture and assemble surface mount devices (SMDs). New manufacturing techniques, equipment and production lines have all helped meet the ever-growing demand for the SOT23 and its derivatives. All the while delivering the consistency and quality our customers demand.
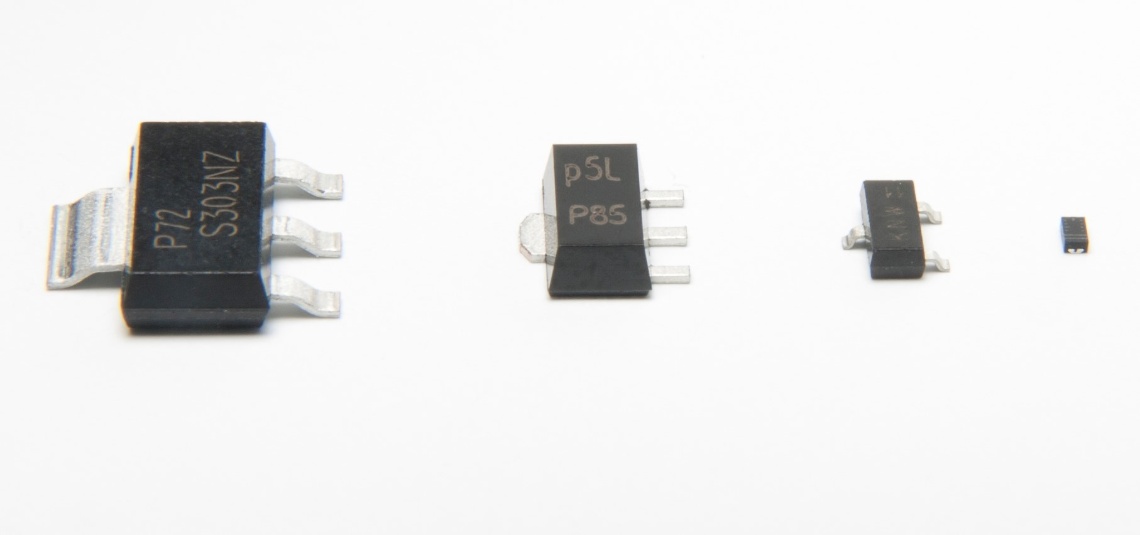
A long way from retirement
While some of us realize that 50 is not quite the new 30, we also know that we are a long way from retirement. The same can be said about the SOT23. Of course, innovation never stands still in the semiconductor industry so where space constraints are at their maximum new very small leadless packages are essential.
But where space is more flexible, when it comes to efficiency, consistency, reliability and cost, the SOT23 holds it head high. The fact that last year we shipped over 30 billion devices housed in SOT23 for use in countless automotive, consumer, computing and industrial applications, and this year we expect to ship more, is testament to that.
While innovation continues to drive us forward, at Nexperia efficiency is at the heart of everything we do. That’s why we have continued to invest in the manufacturing techniques, equipment and production lines that are vital to meet ongoing demand. And for the SOT23 we expect to do so for the next couple of decades.