In the final blog of the series, we take a look at package and MOSFET requirements specifically for 12 V to 48 V DC/DC conversion.
I briefly described the function of power MOSFETs and how they fit in automotive applications such as the motor control of a 48-volt starter generator in “Power MOSFETs – the muscle in 48V systems”. In this final chapter of the series, I explain the benefits of the latest MOSFET packaging solutions and why they should be the preferred choice for most automotive systems. Furthermore, we delve into one of the essential 48-volt systems – the 48 V DC/DC converter – and take a quick look at its basic function and power semiconductor contents.
Power MOSFET packaging – the benefits of copper clip
Traditionally power MOSFET packages were quite significant in terms of size, as this provided better thermal dissipation and performance, increasing overall safety and reliability of the device. Conventional packages such as TO-220, TO-247, I²PAK, DPAK and D²PAK have been used for years and some suppliers still make use of them due to their cost and known characteristics.
However, as automotive electronic systems have become more advanced, power MOSFET devices have had to become more efficient. This has led to the emergence of packages using copper clip bonding technology rather that the wire bonding technology for the MOSFET terminal connections. Copper clip technology provides numerous benefits including reduced total device resistance, improved power density and better switching performance.
One of those package designs, the LFPAK, has gained significant acceptance for many automotive applications since its introduction back in 2003. A major benefit of LFPAK is its improved performance in thermally demanding environments, where the board reliability of the device is crucial. Another key technology factor is the shorter leads (legs) of the device which contribute significantly to the lower inductance and package resistance. The exposed leads also contribute to better stress handling compared to packages such as power quad flat no-lead (PQFN) packages where micro pins are used instead of leads.
Figure 1 shows the package footprint improvement of LFPAK compared to traditional wire-bonded DPAK. It is estimated that a 5 mm x 6 mm LFPAK (or LFPAK56) has less than half of the total footprint of a DPAK while offering lower package resistance and higher power density. For more information on the benefits of LFPAK and its copper clip technology, take a look at this quick learning video.
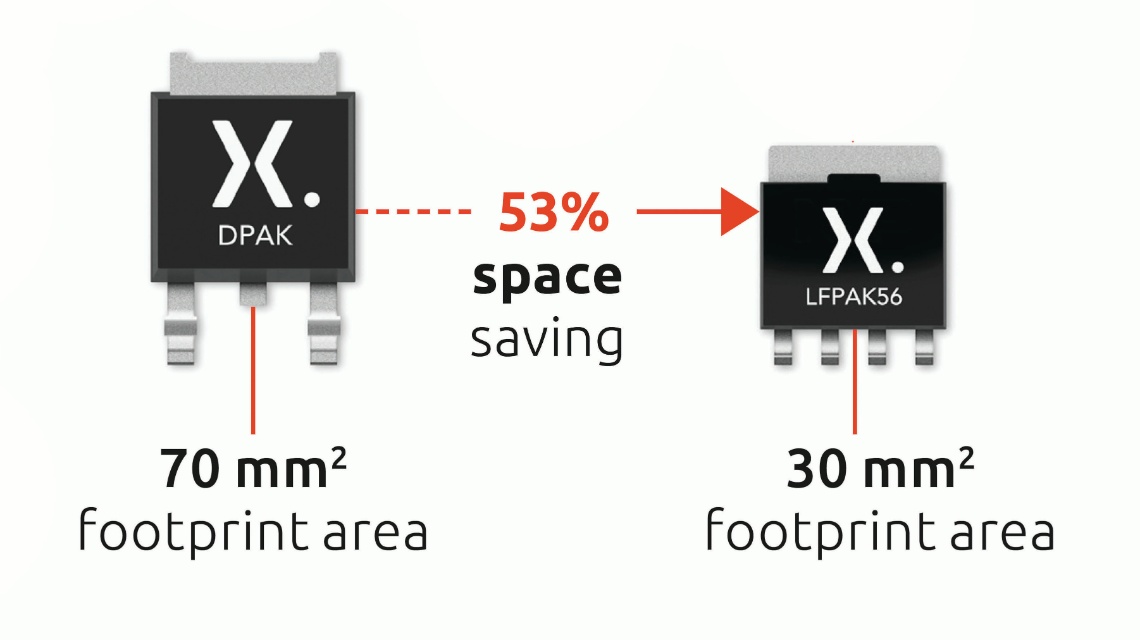
The LFPAK family
After the initial introduction of the LFPAK56, its growing popularity led to the introduction of different LFPAK variants to address the variety of applications. Figure 2 displays the current LFPAK family. At the lower power end of the scale, we have the LFPAK56D (dual channel - two transistors in one package) and LFPAK33 (3 x 3 mm) packages. Both offer significant size reduction and better power density. At the other end, the latest addition to the family is the LFPAK88 (8 x 8 mm) with its 64 mm² footprint. Due to be released in early 2019, this package is aimed at meeting the growing demand of high-power 12-volt applications and of course will address important 48-volt applications including the 48-volt DC/DC converter.
48-volt DC/DC converter
The 12 to 48 V DC/DC converter plays an essential role in 48-volt automotive systems. As its name suggests, it converts the voltage level from the 48-volt bus to the 12-volt one and vice versa. The converter aims to increase the efficiency of the system and provide a stable power supply even when the engine is turned off during start-stop or while the vehicle is coasting.
Figure 3 summarises the converter’s functions between the two voltage levels. In the context of a 48-volt mild hybrid, whenever the belt-starter generator (BSG) recovers energy back to the 48-volt battery, the converter can transfer this power to 12-volt loads. As already mentioned, the converter can also transfer power from the 12-volt battery to start the engine and support the driving functionality during coasting on the motorway.
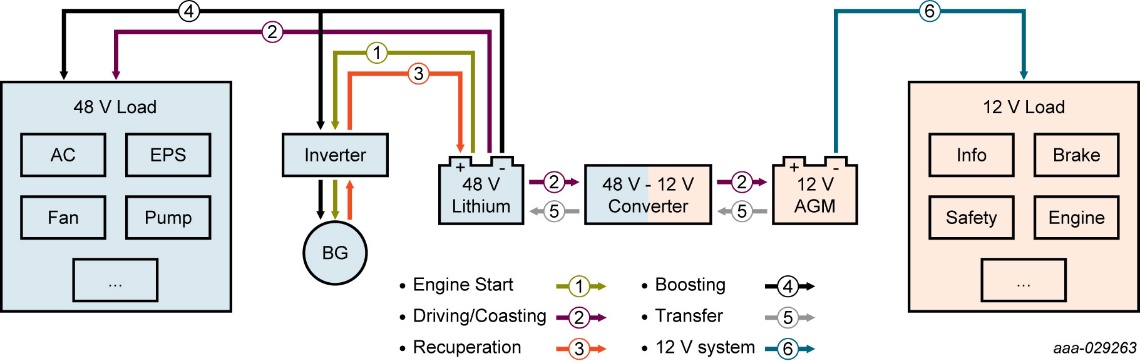
*Some applications such as electrical power steering (EPS) will initially remain on the 12 V bus
Looking at the 48-volt DC/DC converter from a power semiconductor perspective, the converter requires sophisticated MOSFET circuitry for short circuit protection, phase switching and 12-volt reverse battery protection. Figure 4 highlights these main areas and the corresponding MOSFET voltage requirements. Additionally, the MOSFET switches are required to have very low resistance (RDS(on) < 1 mΩ) to reduce losses and be capable of dissipating a significant amount of generated heat.
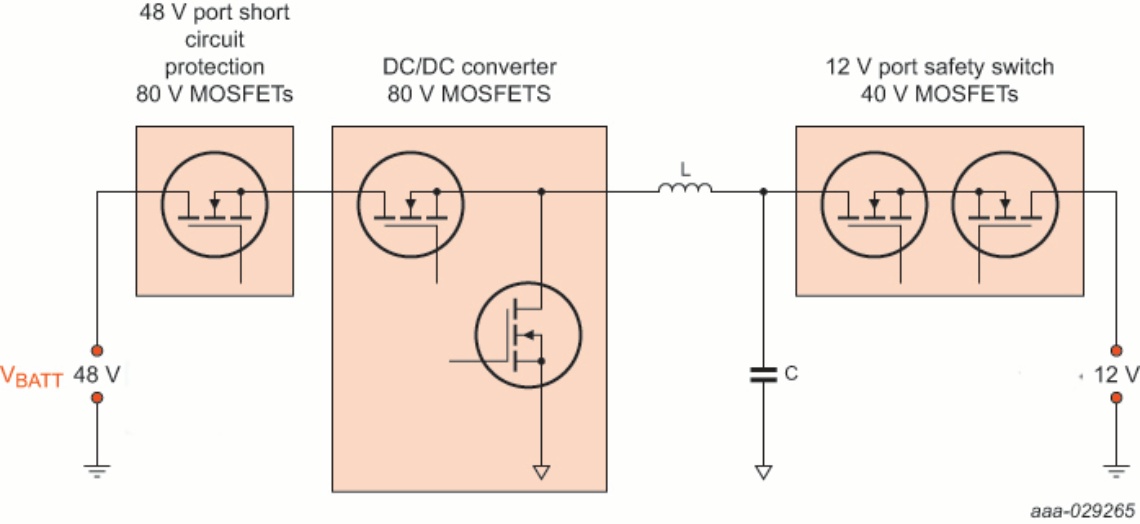
Meeting these demands is possible by using copper clip packaging technology in package solutions such as the LFPAK88, which can reach resistances as low as 0.7 mΩ for a 40-volt device. Furthermore, this 8 mm by 8 mm LFPAK can withstand continuous currents of around 325 Amps.
All in all, systems such as the 48-volt DC/DC converter require significant amount of electronics to be efficient and useful. It is important to note that in addition to the MOSFETs, devices such as diodes and logic gates also play an important role in the overall system.
What the future holds
In this blog series, I aimed to introduce the growing topic of vehicle electrification and how it could impact the automotive and power semiconductor industries. It was important to delve into some of the 48-volt systems and understand how they operate and what requirements they have. There is no doubt that 48-volt will become the new mainstream system in automotive. It will allow internal combustion engine cars to become more efficient by enabling the vehicle’s kinetic energy to be recovered back to the 48-volt battery.
In the long run, the 48-volt system may also be applied to other forms of electrified vehicles such as full hybrids, plug-in hybrids and even fully electric vehicles. From a power semiconductor, more specifically MOSFET point of view, the demand for better and more efficient MOSFETs will continue. Hence, manufacturers need to stay innovative and make sure they keep with the latest technology trends. That is why packages such as LFPAK will play an important role in improving the system efficiency and safety.