As space becomes increasingly constrained in automotive applications, moving to smaller and lighter leadless DFN packages with side-wettable flanks gives designers room to move.
When we think about the modern car, the image of a relatively large, spacious vehicle springs to mind. Depending on the embedded options, modern cars can easily have well over one hundred ECUs. So when we look at how much space is available for electronic systems then we can quickly see how space constrained today’s vehicles really are. This is only set to increase as more advanced driver-assistance (ADAS) and safety systems are incorporated to meet legislative and consumer demands. In fact, for some applications like the car radio, camera modules and radar sensors, space is already at a premium.
One option is to integrate more and more functionality into smaller single chips, but for many features that is neither efficient or workable. So there is also greater demand for small leadless package options to replace the more familiar small outline leaded surface mount packages for diodes and transistors. When you consider that the SOT23 has an occupied area of 9.9 mm2 (3.3 x 3 mm) while the DFN1110D-3’s occupied area is only 1.1 mm2 (1.1 x 1.0 mm), then you can appreciate the potential space benefits.
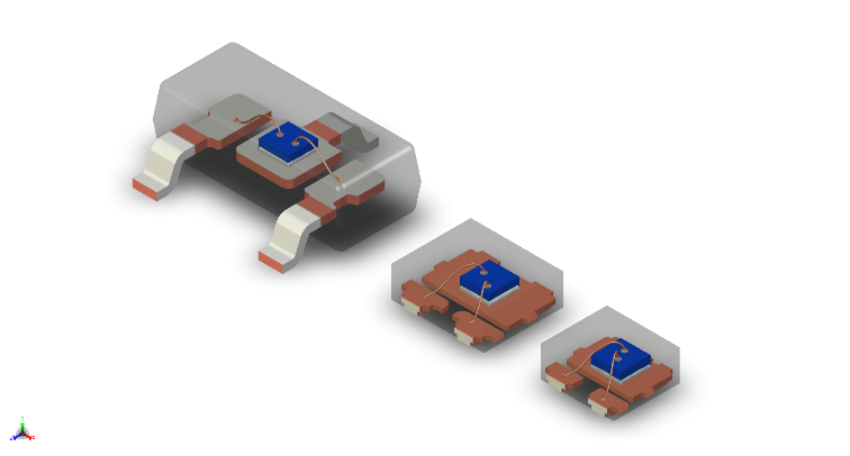
Addressing automotive’s unique challenges
With the pressure on board space, moving to small dual or discrete flat no lead (DFN) options can free up significant room allowing designers to either reduce the overall footprint or increase functionality for the same board space. It also provides cumulative weight savings in an industry where every gram counts. Of course, automotive applications bring their own unique challenges in terms of board level reliability and quality compliance. That’s why packages like the SOT23 (and its variants) remain industry favourite outlines despite being first introduced in the 1960s.
Nexperia has specifically looked at how to address the concerns of the automotive industry and ease the shift to small leadless packages for diodes and transistors. That has meant ensuring all our DFN package options are automotive qualified and meet specific performance requirements. From improved thermal characteristics ensuring DFN packages stay cooler (including at higher Ptot values), being 175 °C temperature rated for under the hood applications and introducing side-wettable flanks (SWF) allows for full automatic optical inspection (AOI) after soldering. Through to providing a broad portfolio of functions and features in a range of DFN footprints to help minimize the cost of switching to DFN-capable pick and place equipment.
We have only just touched on some of the challenges and solutions associated with the shift to small leadless packages in automotive. For example in my blog, 'DFN stays cool under the hood', you can read about how DFN packages better manage thermal behavior.