The sheer volume of automotive electronics in today's cars is dramatically driving up the transmission requirements and data payload on automotive networks. To take the next step we need high-speed, high-bandwidth Automotive Ethernet. And that means getting the right ESD protection in place to ensure it is both safe and secure while we are driving.
As technology continues to evolve, the automotive industry is driven by the major trends of electrification, autonomous driving and shared 'connected' mobility. New applications and technologies have and will continue to significantly increase the data payload that needs to be managed and transmitted in the car, driving up the bandwidth requirements. So existing protocols such as LIN, CAN-FD and FlexRay are no longer sufficient in a heterogeneous in-vehicle network.
Changing the wiring harness to a hierarchical homogeneous network and zonal architecture, and implementing Automotive Ethernet as the global backbone, is expected to reduce cost and cabling weight. It also supports rising demands of high data-rates, data security, and flexibility. However, it means that discrete ESD protection devices are required for high system level ESD robustness and yet fulfill the latest requirements emerging with these trends.
In this series of blogs, we will focus on the new requirements and introduce automotive Ethernet and the specifications of OPEN Alliance for 100 Mbit/s and 1Gbit/s Ethernet. Furthermore, we will discuss the importance and requirements of tailored ESD protection solutions.
OPEN Alliance and ESD protection placement
The OPEN Alliance (One-Pair Ether-Net) Special Interest Group (SIG) is a non-profit alliance of mainly automotive industry and technology providers collaborating to encourage wide scale adoption of Ethernet-based networks as the standard in automotive networking applications. One key goal is to enable the deployment of the existing IEEE 100BASE-T1 / 1000BASE-T1 physical layer specifications with complementing specifications for conformance and interoperability. Moreover, the OPEN Alliance member companies work together to further complete the eco-system with requirement and test specifications for harnesses, switches, ECUs and additional functionalities.
Discrete ESD protection devices take a crucial role when it comes to system level robustness and new requirements needs to be considered. In previous automotive Ethernet implementations, PHY vendors recommended to put a discrete ESD protection device between the CMC and the PHY, if required. When taking a closer look on the arrangement of ESD protection devices within 100BASE-T1 MDI network proposed by OPEN Alliance, a major change can be seen.
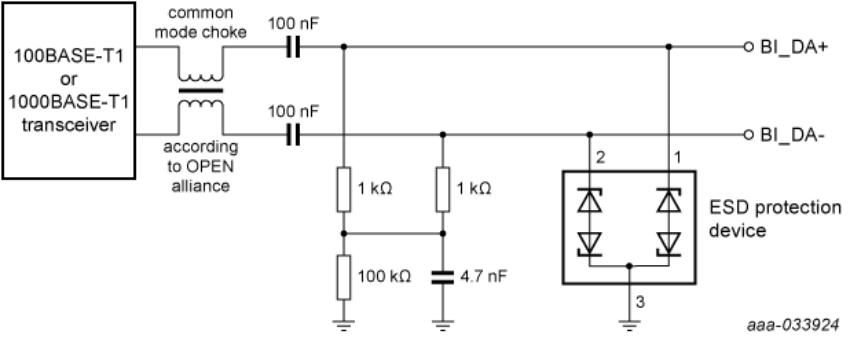
When there is either no ESD protection or it is located at the PHY, then the power of ESD strikes would pass the CM termination, DC Block and CMC. If however the ESD protection device is placed right at the connector the it not only protects the PHY but also the common-mode choke (CMC) and passives. At this position, the power of ESD strikes can immediately be directed to ground however this change in topology requires a completely different ESD protection.
Rethinking protection requirements
Where the ESD protection at the PHY has to have a matching characteristic to the PHYs internal protection, the protection at the connector has to comply with the harsh environment on the cable. For example, cables may be shorted to voltages sources such as the car battery, and they are exposed to high power common mode noise. Therefore the ESD protection devices require an ESD trigger voltage ≥ 100 V and, in addition to IEC61000-4-2 level 4, must withstand a minimum of 1000 discharges. While offering enhanced behavior, ESD protection devices must still offer a high signal-integrity which requires a low parasitic capacitance (less than 3.5 pF).
In the next articles, we will take a closer look on the required tests requested by OPEN Alliance such as mixed mode S-parameter measurements, damage from ESD, ESD discharge current measurement, and unwanted clamping effect at RF immunity. We will explain the measurements we achieved with the Nexperia Reference Design Board and highlight the effect of different ESD protection device concepts.
Detailed information about Nexperia´s 100/1000BASE-T1 Ethernet products, including parametric search and cross reference, can be found here: www.nexperia.com/ethernet