We all know that size matters, but when you need to measure every milliwatt of power or count every gram then the efficiency and weight advantages that LFPAK brings to automotive applications will play an increasingly important role.
Weighing the benefits of LFPAK
It’s likely that you have already heard of the benefits that LFPAK offers designers, with its design and construction optimized to give the best thermal and electrical performance, cost and reliability. The fact that it is now being recognized as the de-facto standard power SO8 package shows the journey LFPAK has been through in the last 15 years. However, one thing that isn’t often talked about is the size and weight advantages that this dedicated package brings to automotive applications and how this will play an increasingly important role.
We all know that space is constrained in every application, and automotive applications are no different. Just look at the amount of electronics squeezed into today’s wing mirrors. There is remote vertical and horizontal adjustment, automatic mirror folding, integrated side indicators, blind spot information systems, and they can be electrically heated and may include electrochromic dimming. To add any more functionality means we need to make space savings. That’s where the footprint advantages of LFPAK come into play, especially with the developments like LFPAK33, LFPAK56D and LFPAK56E.
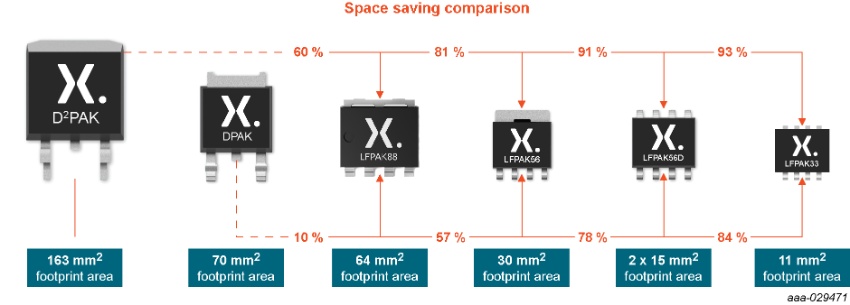
What’s more as the trend towards autonomous driving continues, safety-critical systems must guard against unexpected failure. In systems such as power steering dual redundancy is increasingly being employed, effectively doubling up components and circuits in case anything goes wrong. The result is we are seeing 3-phase motors being replaced by 6-phase and even 9-phase motors, where up to 18 MOSFETs are required along with control switches to ensure effective redundancy.
So it is worth noting that, as well as saving space, LFPAK also saves weight. It’s a lighter package that has a significant weight advantage over DPAK and D2PAK in percentage terms, some 77% and 94% respectively. Of course, in real terms even with over 100 MOSFETs in each car this amounts to only a small fraction of the total weight of a car. But in the automotive industry weight is becoming just as critical as size.
Package |
RDSon (mΩ) |
Weight (mg) |
Weight / car* (g) |
Weight / car* (kg) |
Weight reduction (%) |
D2PAK |
8.1 |
1430 |
142.96 |
0.14 |
0 |
DPAK |
8 |
341 |
34.13 |
0.03 |
-76% |
LFPAK56 |
8 |
80 |
8.00 |
0.01 |
-94% |
LFPAK56D |
2 x 8.7 |
117 |
5.86 |
0.01 |
-96% |
LFPAK33 |
6.3 |
58 |
5.77 |
0.01 |
-96% |
* Assuming a typical car has 100 MOSFETs
Why is weight so important?
Roughly speaking for every 100 kg of vehicle mass, 9 grams of CO2 is produced per kilometer. In 2015, new cars sold in the EU had average emissions of 119.5 g of CO2/km. While this was 8.0 % below the 2015 target, the EU target for 2020/2021 is 95 g of CO2/km for passenger cars.
Simply increasing engine efficiency and the efficiency of both generating and using electrical power, is no longer sufficient. To meet the 2021 EU target it is essential to look at a system level solution. And as the amount of CO2 released is related to the mass of the car, anything that can ‘lighten the load’ is important.
Electric cars weigh in
Severe CO2 emission restrictions are also helping push car makers towards more electrified cars: either full electric or hybrid. Does this mean saving a few grams here or there will matter? The simple answer is ‘Yes’. In fact, if there is any doubt over the importance of minimizing weight, then the rise of the electric car settles the argument. The heavier the vehicle, the more power needed to make it go, and the more drain on the battery. Therefore range – one of the key limiters of eCar appeal – is reduced.
The goal is to spend as few Watts per kilometer as possible. So making electric cars lighter remains a key challenge for designers. Power MOSFETs in LFPAK bring many benefits to vehicle systems and perhaps weight-saving is not the most obvious.
Nonetheless, in the automotive industry, every gram counts.