For many decades, Ethernet has been used in industrial and computing networks but nowadays it is increasingly being deployed in automotive applications as a replacement for legacy networks like Controller Area Network (CAN). Automotive Ethernet offers the topology flexibility, high bandwidth and robust communication required for in-vehicle data communications as original equipment manufacturers (OEMs) transition from domain to zonal network architectures. This article discusses various automotive Ethernet standards before considering the stringent electrostatic protection (ESD) and electromagnetic compatibility (EMC) standards they are required to comply with. Finally, it presents a range of components from Nexperia which automotive OEMs can use to ensure that vehicle networks are fully protected against ESD events.
Automotive Ethernet standards
In 2016,100BASE-T1 and 1000BASE-T1 automotive Ethernet were developed by the One Pair Ethernet Network (OPEN) Alliance committees (and subsequently standardized by the IEEE), to address specific requirements of automotive applications primarily related to electromagnetic interference (EMI) and compatibility (EMC). 10BASE-T1S was developed in 2020 to enable short-distance multi-drop network topologies, a feature which makes it ideally suited for supporting vehicle zonal architectures. A multi-gigabit version (MGBASE-T1) of automotive Ethernet, is currently in development. The specifications for each of these standards are shown in Table 1.
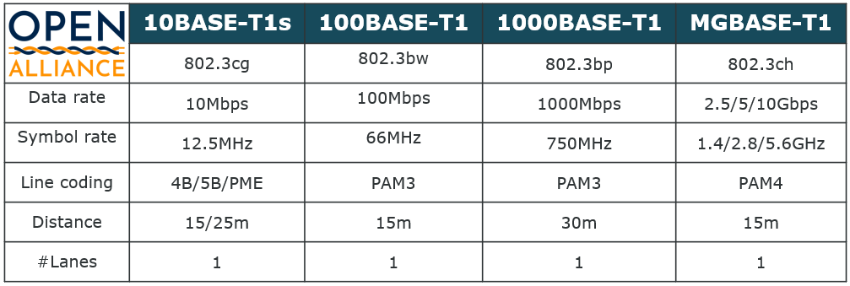
Protecting Automotive Ethernet Networks
Unlike versions of Ethernet deployed in computing installations, the 10BASE-T1s, 100BASE-T1, and 1000BASE-T1 automotive Ethernet standards use a single unshielded twisted pair (UTP) of cable to connect physical layer interfaces (PHY) as shown in Figure 1. UTP cables are smaller, lighter, less expensive and easy to use – key requirements for automotive OEMs, but their construction presents additional challenges for protecting against EMI.

In modern vehicles, hundreds of meters of cable connect multiple electronic control units (ECUs) managing various functions. Cables are typically bundled together in wiring harnesses and this significantly increases the possibility of problems relating to EMI. In worst-case scenarios, EMI voltage amplitudes can reach up to 100 V in UTP cables so Ethernet networks must be sufficiently robust to withstand these peaks. Protection circuitry specified by the OPEN Alliance for each node in an automotive Ethernet network is shown Figure 2. This includes a common mode choke (CMC) to filter unwanted common mode noise that can couple onto the cables, while also helping to protect against the potentially damaging effects of ESD.
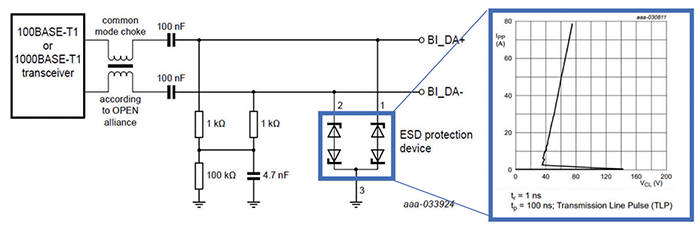
Key requirement for the ESD protection device is that it should not activate at voltage levels below 100 V, while providing at least 15 kV of ESD protection (for a minimum of 1000 discharges) for an operating voltage of 24 V. The OPEN Alliance also recommends a series of additional tests for OEMs to perform and while these are broadly similar for 100BASE-T1 and 1000BASE-T1, they have different passing criteria. Two of these tests are designed to measure the impact of an ESD protection device on signal integrity (SI) and measure insertion loss (IL), return loss (RL), and common mode rejection ratio (CMMR). An ESD discharge current test quantifies the current flowing into a PHY during an ESD event, while an RF clamping test is designed to ensure a node has EMC up to 100 V. For the 10BASE-T1s, there is an additional test of the device capacitance to ensure the total capacitive load of the node is not critical.
For practical automotive Ethernet deployments, the placement and layout of the ESD protection is crucial. As shown by the field scan image in Figure 3, this should be located at the connector to ensures that the ESD pulse is clamped to ground directly at the connector, to provide maximum protection for all of the network circuitries including the CMC, and the PHY.
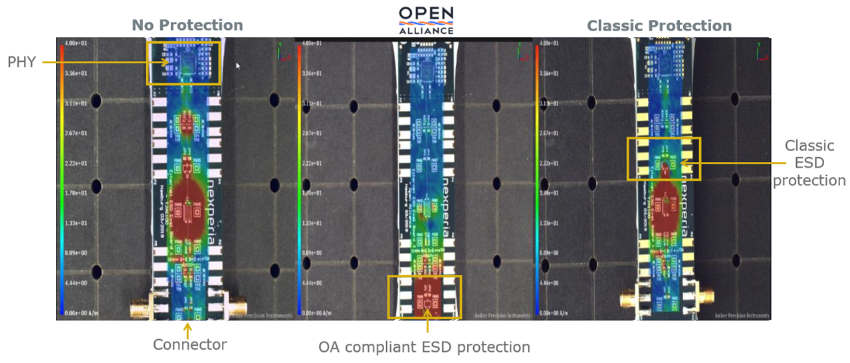
The CMC reduces the ESD stress on the PHY under pulsed conditions. When a transient hits the CMC, it blocks the current for a period which depends on the voltage level of the pulse - the higher the voltage, the shorter the blocking phase. The blocking phase is followed by a saturation phase where, the CMC behaves like an inductor being driven into saturation. Once it saturates, it then begins to conduct the current and the voltage across the CMC starts to fall. ESD device package routing should always be straight, avoiding any stubs or bends and line traces for differential signals should pass over the pad of the ESD device. For signal integrity reasons, stubs should be avoided, and the impedance of the differential lines should be 100 Ω. This can be achieved by keeping the line separated. Nexperia’s recommended routing options for different package types are shown in Figure 4.
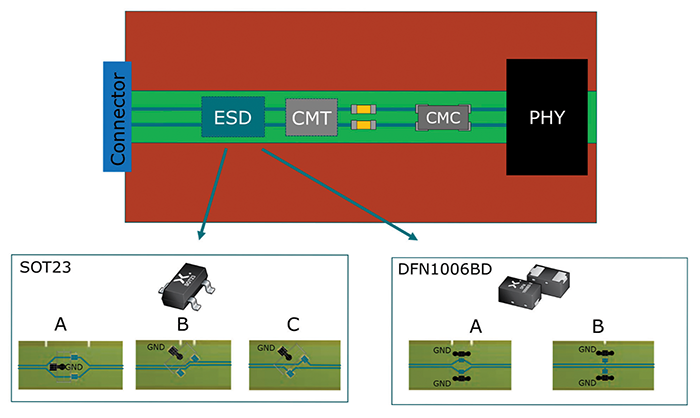
Nexperia offers a Comprehensive Range of ESD protection devices for Automotive Ethernet
Nexperia offers a wide selection of ESD protection devices for automotive Ethernet networks (Table 2). The PESD2ETH range devices fully OPEN Alliance 100BASE-T1 compliant and come in a small SOT23 surface-mounted plastic package designed to protect two automotive in-vehicle network bus lines from damage caused by ESD and other transient events. PESD1ETH1G devices are OPEN Alliance IEEE 100BASE-T1 and 1000BASE-T1 compliant and come in a small DFN1006BD-2 (SOD882BD) surface-mounted plastic package.
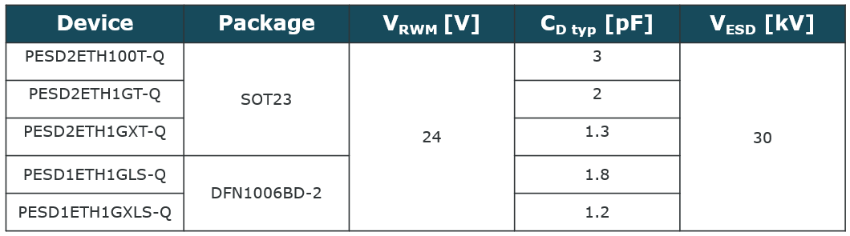
Nexperia also offers the high robustness OPEN Alliance compliant 10BASE-T1s devices shown in Table 3. These have a trigger voltage (Vt) which exceeds 100 V low device capacitance (< 0.5 pF) to enable smooth data transmission and good signal integrity. They have a capacitance matching specification of 2% (maximum) for dual line packages. These devices are also 100BASE-T1 and 1000BASE-T1 compliant. Additionally, the parts are also specified with 75 V VRWM, making them suitable for use in 12, 24 and 48 V board-net systems.
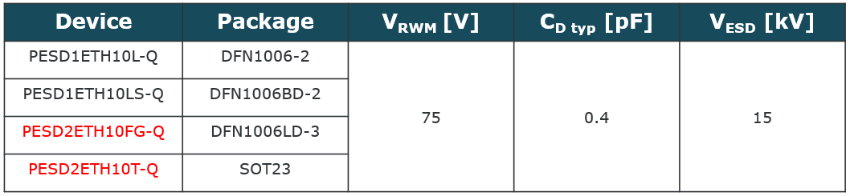
Conclusion
The article discussed the protection requirements for automotive Ethernet networks and presented board layout options to help improve robustness against ESD and EMI. Whether implementing 100BASE-T, 1000BASE-T or 10BASE-T1s, automotive OEMs can rely on Nexperia to provide protection devices with the specifications and form factors they need for their in-vehicle networks. To discover the full portfolio, visit nexperia.com/automotive-ethernet.